Meget vellykket bedriftsbesøk 14.10.2022
Fabrikksjef og medlem av Røyken RK, Erik Ølstad, tok i mot 16 fra klubben, orienterte om bedriften og ledet «guided tour» gjennom produksjonslinjen av Rockwool isolasjonmatter.
Fra notatblokken gjengis:
Steinull lages av stein som smeltes i en ovn ved 1 500 oC. Steintyper som brukes som råstoff er basalt, dolomitt og gabbro. Dolomitt inneholder tremolitt (asbest) som filtreres ut. Bedriften har gjort meget store investeringer for å effektivisere og redusere utslipp av CO2 og lystgass rensing av (dinitrogenmonoksid, N2O).
- Stein består av mineraler, herunder jern som tappes ut fra bunnen av smelteovnen.
- Hovedinvesteringen er smelteovn som benytter elektrisitet som energikilde. I den forbindelse ble det bygget en ny trafostasjon som Rockwool finansierte.
- Den gamle smelteovnen benyttet koks (i biter på 150-250 mm) som energikilde og trengte 20 000 m3 luft i timen for å holde fyr på 1 400-1 500 kg/time koks og som ble kilde til store CO2 – utslipp (når 1 kilo koks forbrennes genereres drøye 3 kg CO2. I tillegg til CO2 blir det også utslipp av metan (CH4) og lystgass (N2O))
- Overgangen fra å bruke koks i produksjonen og til å installere en ny elektrisk ovn har ført til at selskapet kutter CO2-utslippene med 80 prosent, i tillegg til å redusere avfall til deponi med 95 prosent.
- Investeringen medførte at Moss’ samlede utslipp av klimagasser ble redusert med ca. 15 %.
- Det tas inn 85 000 tonn stein pr. år, som omdannes til 65 000 ferdige steinullprodukter.
- Stein som leveres er ferdig knust til 3 – 15/20 mm grus.
- Ca. 35% av steinen leveres fra steinbruddet i Filtvet og transporteres med lastebil; dvs.ca. 30 000 tonn årlig. Bruk av båt er ikke et alternativ pga. kostnadskrevende omlastinger fra bil til båt og vice versa.
- Steinull kan gjenbrukes og fabrikken satser stort på å motta brukt steinull fra riving av bygninger etc. som råstoff.
- Ferdigvarer transporteres til lager ved Vålerveien med to lastebiler som går i skytteltrafikk der den ene lastes opp mens den andre er «på tur», så sjåføren kan veksle fra den ene til den andre.
Bedriften har ca. 100 ansatte og kjører 6 skift i døgnet med 10 personer pr. skift. Produksjonen er helautomatisert, og det var imponerende å se «overvåkningssentralen» der 1 person styrer det hele, fra smelting, spinning frem til ferdige isolasjonsplater.
Klubbens nestor og chartemedlem Ove Blakset sa da det hele var over: «Jeg har vært på mange bedritsbesøk i løpet av mine 50 år i klubben, men dette har vært det beste!»
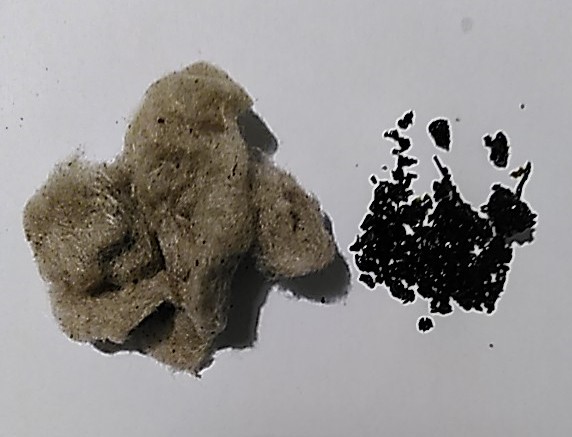
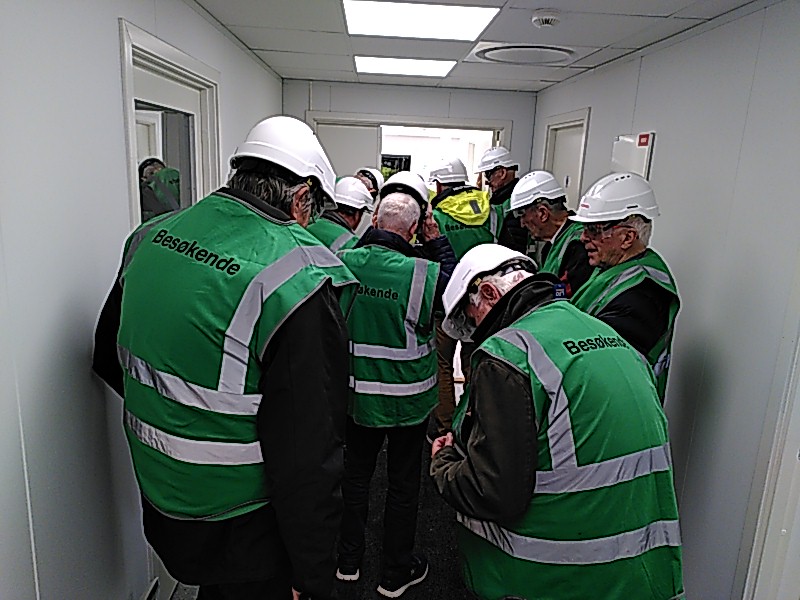
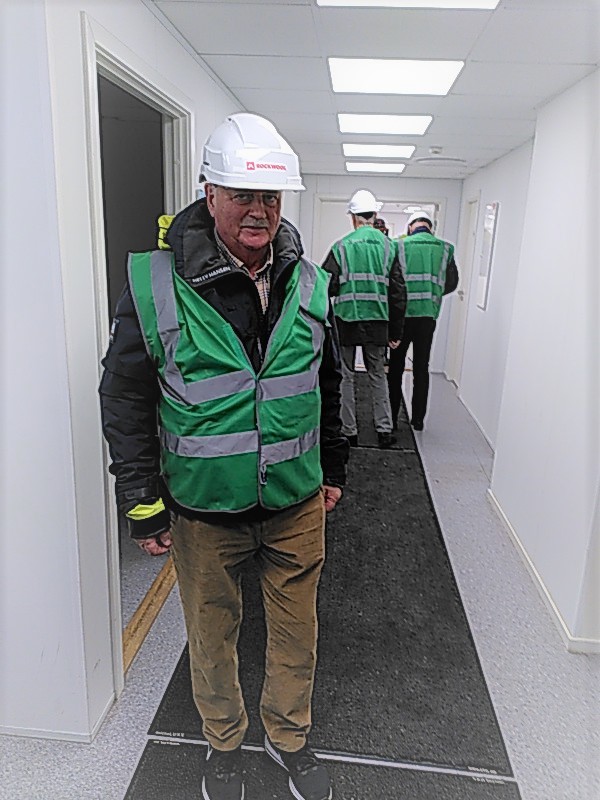
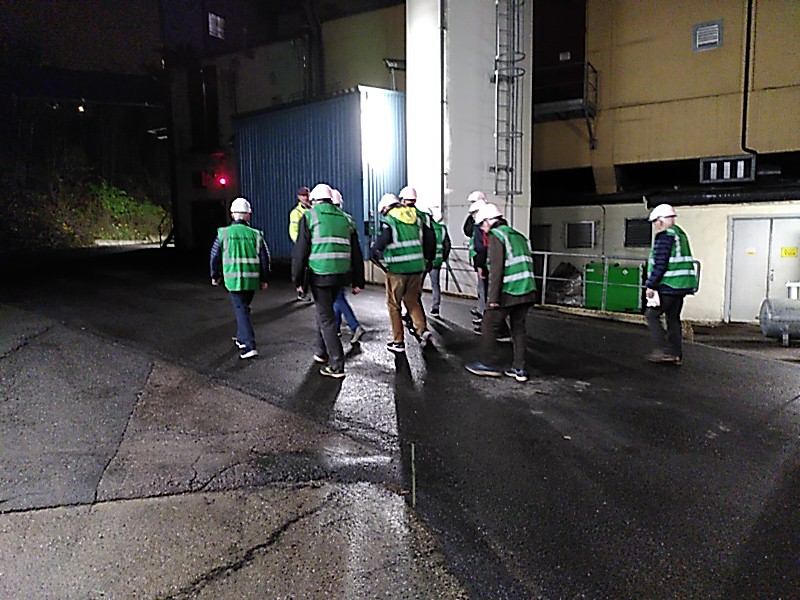